Applications
Wide range of applications, including gasoline and diesel HDT, Cat Feed HDT, Mild HCK, etc.
Tailored design for each reactor for optimum performance and flexibility
EquiFlow® trays and 300 quench systems awarded worldwide
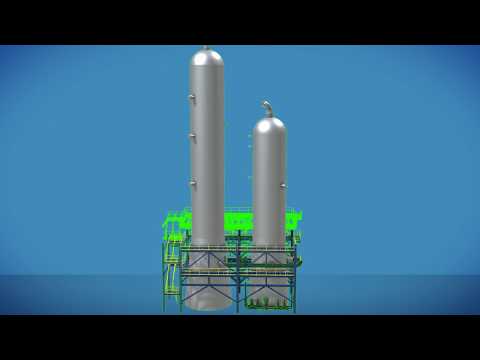
EquiFlow® is the latest generation of reactor internals for hydrotreatment reactors. Its purpose is to provide excellent flow distribution starting at the inlet of the catalyst bed in order to maximize the efficiency of the catalyst.
The implementation of EquiFlow® technology maintains a perfect gas/liquid distribution through the catalytic bed to guarantee the performance while also maximizing the cycle duration. The principle is to ensure an optimized mixing of the gas and the liquid phases before entering the catalytic bed ensuring that the entire reactor the catalyst inventory is acting efficiently.
EquiFlow® distributor trays
EquiFlow® distributor trays employ a dispersive system located below a chimney tray to ensure close-to-ideal vapor/liquid distribution throughout the catalytic bed underneath.
Depending on the application, several options are available:
- Hy-Tray™ is the latest generation of trays, with improved efficiency in terms distribution.
- In addition, Hy-Clean™, a smart filtering tray system has been developed for services that are prone to fouling.
- Hy-Mix™, Hy-Sep™ and Hy-Up™ for selective hydrogenation services
- Hy-Quench XM™
- Hy-Quench-NG™
EquiFlow® Reactor Internals portfolio
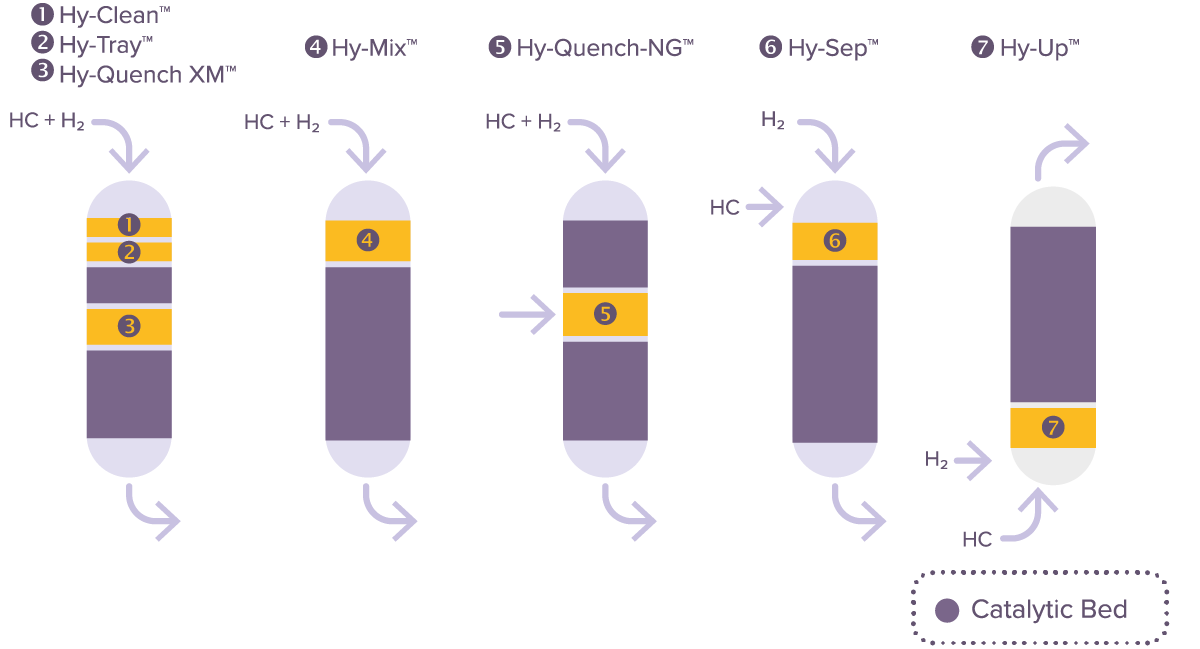
Temperature profile with conventional tray vs near ideal temperature profile with EquiFlow® tray
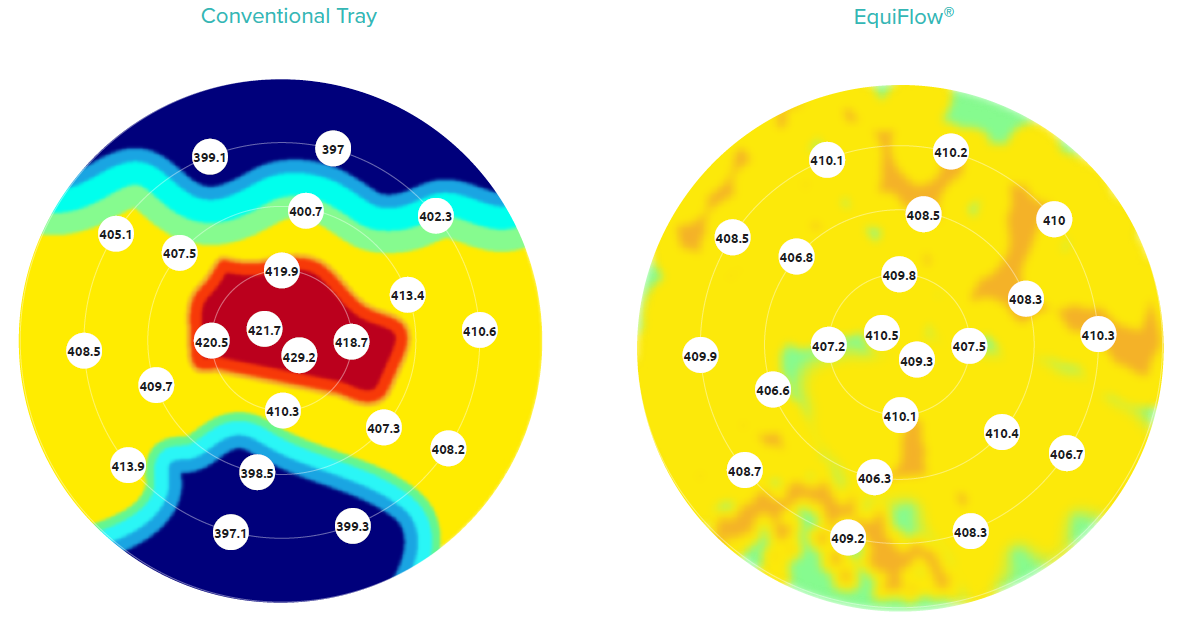
EquiFlow® Distributor Trays for Selective Hydrogenation Services
Combined with SeLene™, Axens family of selective hydrogenation catalysts, Axens proposes a unique and effective solution to boost unit performances.
EquiFlow® Quench system
The EquiFlow® quench system is designed to perfectly mix the effluents from the upper catalytic bed with a quench stream injected into the reactor. The mixture is then uniformly distributed before entering the lower catalytic bed.
Hy-Quench-XM™, Hy-Quench-NG™ are new quench systems featuring a more compact design offering the possibility to load more catalyst within a given reactor volume, while improving the gas/liquid mixing.
The Hy-Quench-XM™ is dedicared to hydroprocessing services, and the Hy-Quench-NG™ to selective hydrogenations which are suitable where exothermic reactions occur.
Key advantages:
- Compact installation
- Wide range of operating conditions
- Homogeneous Gas/Liquid mixing for better catalyst efficiency
You Might Be Interested In
Catalyst Protection Systems
Resources
How can the FCC unit be upgraded to benefit petrochemical integration?
Case Study - Enhancing diesel hydrotreater capacity and reducing CO₂ emissions
What areas of expertise are needed to mitigate constraints in plant/facility staffing levels?
Case Study - Multi-sites Energy Efficiency Audit in the Framework of the ISO 50001 Standard
Technical Article - Use Real-Time Optimization For Low-Sulfur Gasoline Production
How can the FCC unit be upgraded to benefit petrochemical integration?
What areas of expertise are needed to mitigate constraints in plant/facility staffing levels?
Besides improved catalyst systems, what advances in reactor internals are improving efficiency and throughput while also mitigating the effect of fouling and catalyst poisons?
How has the integration of alternative feedstocks impacted your overall energy efficiency (any pluses and minuses)?
Axens and ZPJE established Nectis: a joint-venture dedicated to the promotion and sale of Spiral Tubes Heat Exchangers
Axens Selected for Byco’s Refinery Upgrading Project Phases I, II & III to Support in Producing Euro V Gasoline and Diesel, Pakistan
Axens will supply technology for Alpha-Olefins production to Baltic Chemical Plant
Axens selected for BUA Group integrated refinery and petrochemical project in Nigeria
TO CONTACT US
Please fill in the contact form below