Future of Air Travel
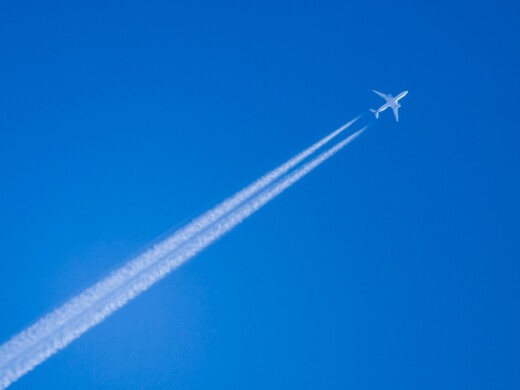
Transport emits nearly 8 Gt of carbon dioxide (CO₂) each year or 30% of global CO₂ emissions (IEA, 2023), 0.89 Gt being emitted by aviation transport. Urgent actions are required to meet future demand while lowering the carbon intensity of transport fuels and chemicals. The use of renewable and alternative feedstocks (such as municipal waste, second-generation vegetable oil, and forestry residues) will play an increasing role in this transition.
Processes Overview
Depending on local resources, various solutions can be adapted, ranging from integrating with existing assets to establishing greenfield plants. We provide a single point of contact throughout the execution, integrated guarantees, and process optimization to enhance profitability, enabling a smooth energy transition.
Axens Pathways
Vegan® is a flexible solution to produce renewable diesel and SAF through the hydrotreatment of a wide range of lipids. This technology allows producers to effectively address environmental regulations, sustainability targets, and secure energy diversification with drop-in premium-quality products.
Vegan® technology includes a hydrotreatment section to deoxygenate and remove contaminants from renewable lipids in the presence of hydrogen to produce linear paraffins.
Vegan® technology includes a hydroisomerisation section to upgrade the linear paraffins produced in the previous step into real drop-in middle distillate biofuels. The hydroisomerisation section can be tuned to produce different grades of jet fuel or diesel fuel, according to market needs, with the ability to produce anywhere from 0 to 100% of the middle distillate product as SAF.
Gasel® technology converts synthesis gas (H₂+CO) from various origins – biomass, captured carbon oxides – into a flexible slate of ultra-clean liquid fuels (XTL), including SAF. This Fischer-Tropsch (FT) route is commonly accepted as one of the most promising mid-term solutions for the production of alternative fuels and petrochemicals, including biomass-to-liquids (BTL) and efuels.
If required, this step aims at ensuring a syngas purity suitable for the FT catalyst. It can treat syngas from any conventional acid gas removal process.
The reaction takes place in a three-phase slurry bubble column (SBC) reactor where syngas is brought into contact with the solid FT catalyst to produce long-chained liquid hydrocarbons. The liquid products are recovered in Liquid/Solid and Gas/Liquid separators and sent to the upgrading section.
The raw FT liquid product is stabilised, hydrotreated (olefins and oxygenates), hydrocracked, and isomerised. The fully converted product is then separated, and it offers flexibility towards different production modes (max kerosene or max middle distillates/diesel with a small production of naphtha).
BioTfueL® technology unlocks SAF and advanced biofuels production from energy crops, agricultural, and forestry residues (including wood industry residues) via a thermochemical pathway. This technology is the most de-risked Gasification-FT chain in the market thanks to its successful operation of 2 large-scale demonstration plants in France. Axens is the single licensor for this proven and robust BTL chain. BioTfueL® offers the unique one-stop-shop concept of one-single guarantee from Biomass to SAF!
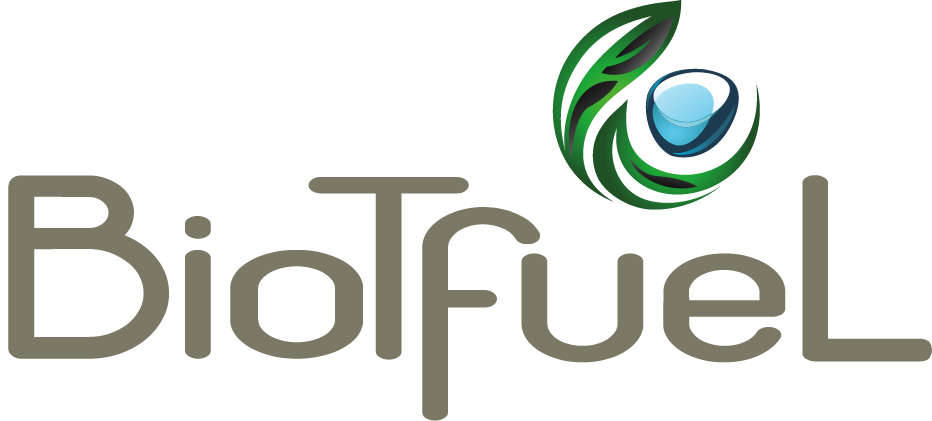
Biomass is conditioned with drying and torrefaction. These steps homogenize feedstock quality, facilitate grinding, and increase storage stability and biomass energy density. Flexible process conditions allow adjustments due to changes in biomass quality and supply strategy.
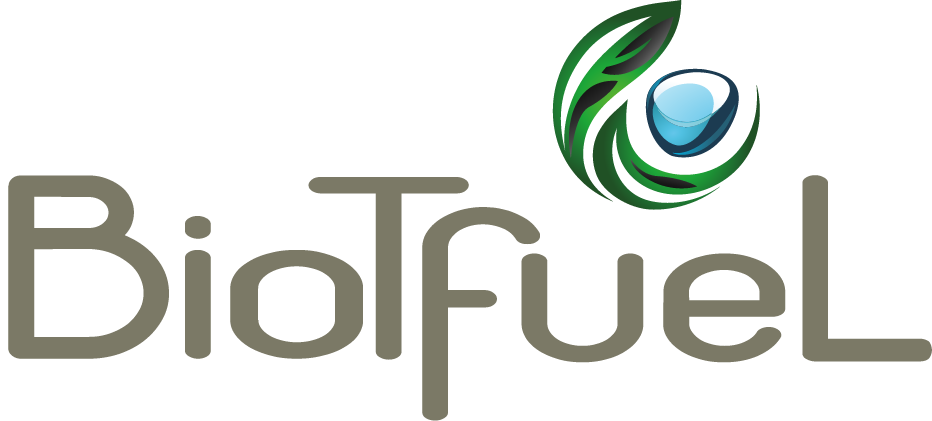
The applied Uhde entrained-flow gasification process with direct quench (PDQ) is a high pressure and high temperature partial oxidation converting carbonaceous material into tar-free syngas.
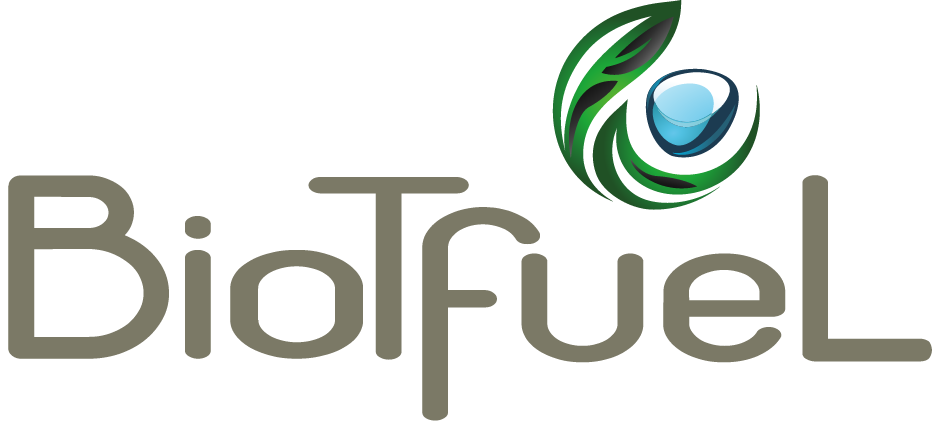
Syngas is conditioned to FT requirement by adjusting the H₂/CO ratio via a water gas shift reaction, followed by acid gas removal and a final purification.
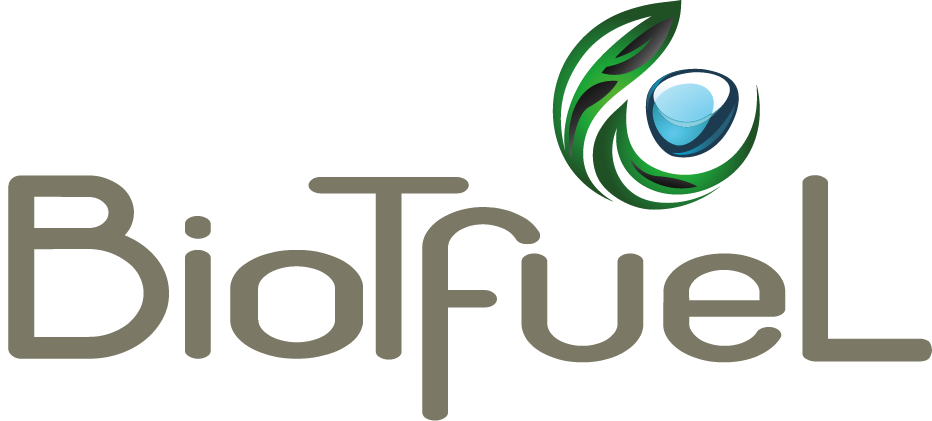
Gasel® technology uses CO & H2 building blocks to form long chains of liquid hydrocarbons. The reaction takes place in a 3-phase Slurry Bubble Column (SBC). The SBC allows perfect control of the high exothermicity and good homogeneity of the reaction. FT products are then upgraded toward the targeted products.
Futurol® converts lignocellulosic biomass from various origins into cellulosic ethanol (advanced bioethanol). This cellulosic ethanol can then be converted to SAF with the Jetanol™ (ATJ) process.
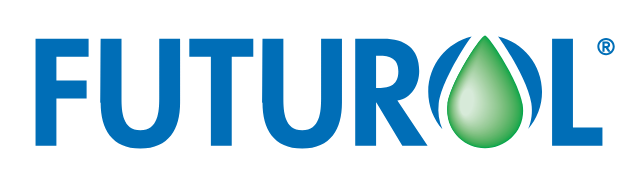
An energy-efficient, single train, continuous technology was selected and optimized for converting biomass feedstock such as energy crops, agricultural, and wood residues to a standardized pretreated substrate, highly digestible, and with low moisture. High hemicellulose conversion is attained while product degradation is minimized.
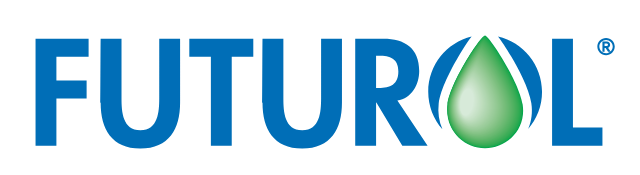
Inhibitors-resistant tailor-made biocatalysts (enzymes and yeasts) were designed, adapted, and improved to optimize process performances. Futurol® offers on-site enzyme production and yeast propagation using lignocellulosic substrate, which strongly contributes to ethanol production cost reduction.
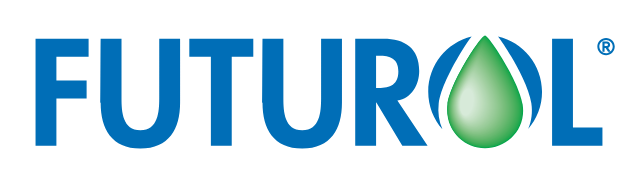
Enzymatic hydrolysis of biomass and co-fermentation of C₅ and C6 sugars take place simultaneously in the same vessel (‘one-pot’ process). This process configuration capitalizes on a synergy between biocatalysts and allows for both Capex and Opex minimization while achieving high ethanol yield through full conversion of C5 and C6 sugars.
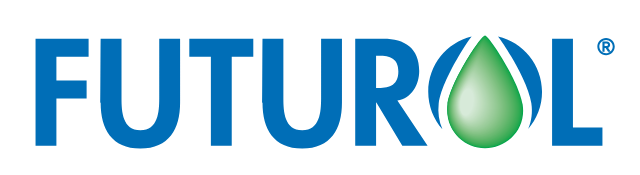
State of the art distillation and dehydration allow recovery of advanced bioethanol suitable for biofuel applications or further processing in chemical production. Lignin and stillage are recovered and routed to energy production while water is recycled.
Jetanol™ is the process by which low-carbon ethanol (bioethanol and advanced bioethanol) is converted to SAF via different steps. This differentiating technology bundle approach utilizes commercially proven processes.
Polymer-grade ethylene is produced by ethanol dehydration (Atol®).
The Ethylene is then oligomerized into SAF utilizing stable catalysts which can be generated and/or on the fly changeout when required.
A last step of hydrogenation is necessary to reduce the olefin content of the product to fulfill ASTM specifications for the final products.
Combining Futurol® and Jetanol™ processes provides the possibility of producing ultra-low CI – or even carbon-neutral, SAF from lignocellulosic biomass.
Resources
Sustainable Aviation Fuels Brochure
Vegan® Commercial Bulletin - Biofuels From Renewable Oils & Fats
Gasel® Commercial Bulletin - Alternative Fuels from Biomass, Waste & Gas
Jetanol™ Commercial Bulletin - Bio Sourced Alcohol Conversion Solution for the Aeronautic Industry
BioTfueL® Commercial Bulletin - Biomass To Liquids (BTL) Solution for Advanced Biofuels
Technical Article - Connecting the Dots to Bankability with Low-Carbon Bio-Hubs for Sustainable Fuels and Chemicals
Technical Article - Fueling the future of aviation – the role of low-carbon hydrogen in SAF production
Video - Axens 700 Series - Catalysts Dedicated to the Hydrotreatment of Pyrolysis Oils and Renewable Fuels
Technical Article - Futurol®: Connecting the dots to bankability with low-carbon bio-hubs for sustainable fuels and chemicals

Case Study - Producing Renewable Liquid Products From Different Lipid Feedstocks Through a Revamp
Read more
Case Study - Feasibility Study Of A Standalone Biorefinery For MGH Based On Axens’ Biofuel Technologies Portfolio Vegan® And Futurol™
Read moreTechnical Article - Connecting the Dots to Bankability with Low-Carbon Bio-Hubs for Sustainable Fuels and Chemicals
Technical Article - Fueling the future of aviation – the role of low-carbon hydrogen in SAF production
Technical Article - Futurol®: Connecting the dots to bankability with low-carbon bio-hubs for sustainable fuels and chemicals
Technical Article - Decarbonising the Aviation Industry
How can the refining industry supply the aviation industry’s growing demand for sustainable aviation fuel (SAF)? What are the most efficient pathways?
What’s the range of drop-in fuels we could potentially produce from biofeedstocks (lipids) with an appropriate process line-up?
Axens tapped for 3 new Vegan® licenses by Galp, LOKEN and SAFCO Ventures, for SAF and Renewable Diesel Production
SAF: KazMunayGaz and Axens extend collaboration
E-fuels: Axens, Paul Wurth (SMS group) and IFPEN sign an agreement for the co-development of the Reverse Water Gas Shift technology
ECARU, Qalaa Holdings and Axens to Carry Out Technical and Economic studies for a Project of Second-Generation Biofuel (Advanced Bioethanol) and Sustainable Aviation Fuel (SAF) Production

Video - Axens 700 Series - Catalysts Dedicated to the Hydrotreatment of Pyrolysis Oils and Renewable Fuels
Read more
Video - E-BioTfueL- A Versatile and Integrated Solution Combining the Best of Biomass To Liquids and E-fuels Worlds
Read more
Video - Take-Kair, Decarbonizing the Industry & Producing SAF to Support the Aviation Sector
Read moreGet in Touch with Us!
Have questions about our offers and solutions or need assistance? The Axens team is here to help. Just a message away!
